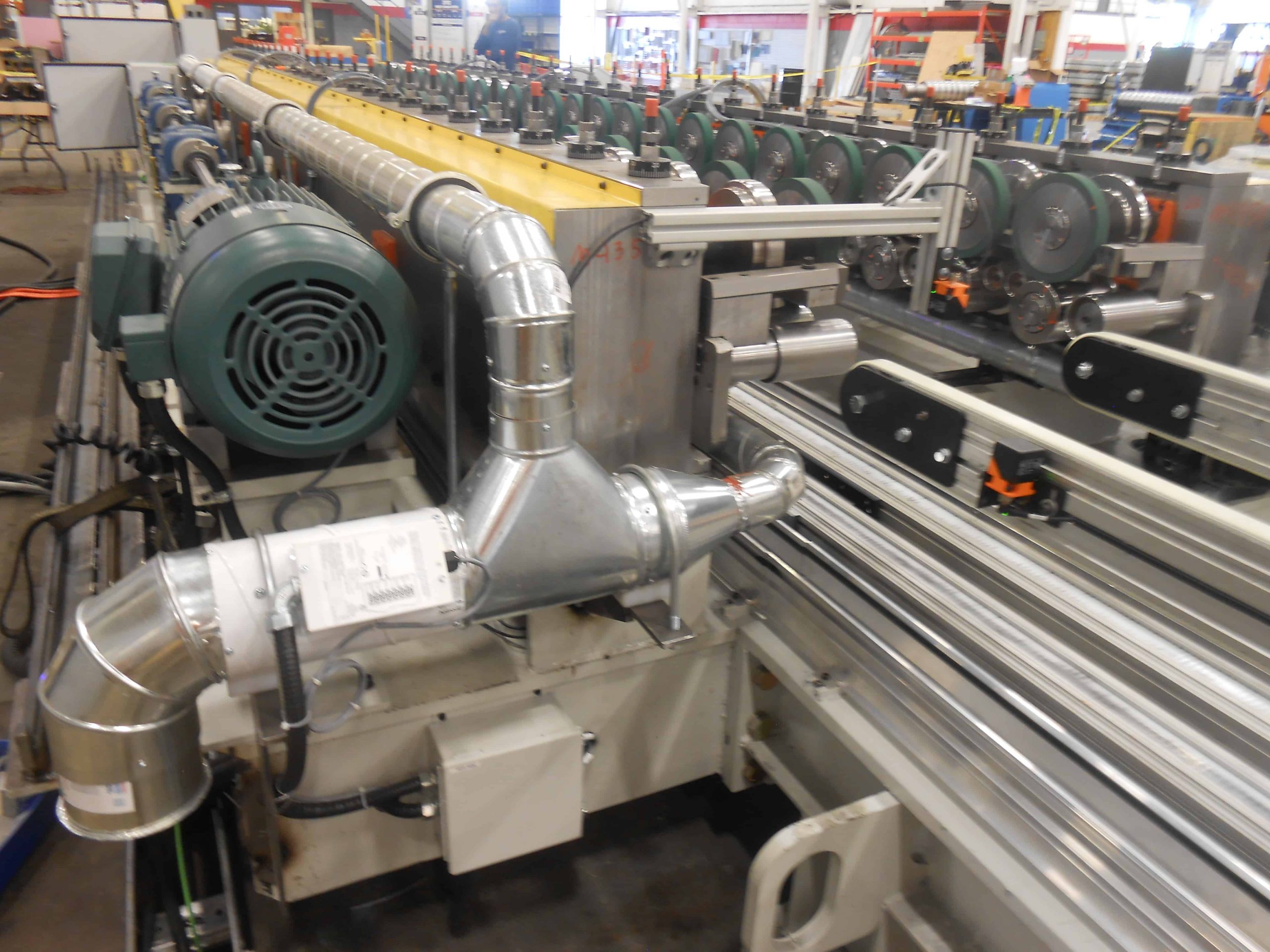
Simplifying the placement of Induction Motors or Servo Motors in your line
By Jim Harmer, Electrical Designer, Samco Machinery
TORONTO, August 16, 2018 – Custom-designing and manufacturing equipment for an entire roll forming line requires a thorough understanding of the multiple applications contained within that line. Engineering these machines to perform to customer requirements can be a challenging process.
Among the considerations during the design process is motor selection for each and every application. From a stand-alone roll former to a roll forming line featuring an uncoiler, flattener, roll former, stacker, nester and packaging station, the motor is what makes the machine run efficiently for the customer.
There are many elements to consider when choosing the type of motor to use.
· Motion Profile
· Torque
· Inertia Matching
· Required acceleration and deceleration time
· Control system architecture
· Cost
· “Real Estate” available on system
Induction motors are common on roll forming applications, conveyor systems, pumps and fans. These systems will typically run at maximum speed and may or may not require the use of a variable frequency drive (VFD). If a VFD is not used, these systems will use a contactor/overload and will run at maximum speed.
A servo motor, on the other hand, is a better option for any application, like punch patterns, different dies, where positioning is key. A servo motor also provides feedback, letting the operator know when proper positioning has been achieved.
Differences between Servo motor and Induction motor:
Servo motor
· Permanent Magnet
· Smaller size than an induction motor
· Able to maintain full torque at low speeds
· More efficient
· Aggressive acceleration/deceleration times
· Feedback of rotor position by resolver or encoder
· Always requires a drive
· Extreme Precision and Repeatability
· Low inertia
Induction motor
· Electromagnets produce a rotating field
· Typically, lower ‘cost’
· Larger physical size
· Less efficient
· Some applications can be controlled without a VFD (variable frequency drive). (Contactors used instead)
· Will not have full torque at low speeds
· Feedback is optional: Incremental encoder or resolver
Understanding the capabilities and flexibilities of these motors goes a long way to designing and producing the best equipment. At the risk of oversimplification, induction motors are generally used for speed control and servo motors are typically used for applications that require dynamic speed and/or position control.
Usages in Roll Forming
Induction motors with a VFD are used on most roll forming applications. They offer the torque required to form the material yet typically do not require aggressive acceleration or deceleration times. The induction motor can run the line at variable speeds; however, will typically run at the maximum set speed until the operator intervenes (roll formers often run at 300 feet per minute or over.) The Induction motors allow for a straightforward setup, operation and maintenance.
A flying punch or shear will catch up to the speed of the material, perform its function and return back to the home position. Flying shears can be controlled by an open-loop system (pneumatic/no motor) or a closed-loop system (servo). A servo controlled flying shear uses the feedback from a line encoder to determine the speed of the roll former. The servo will accelerate to the speed of the roll former, perform its operation while maintaining a synced speed with roll former, and then return to the home position. The servo is able to achieve the acceleration/deceleration speeds necessary for this operation to be successful.
In a rare application, a servo motor would be used for the roll former where you have a standing shear or punch application that requires the machine to stop for the shear or punch.
Usages in Material Handling
Uncoilers and flatteners will generally be driven by induction motors because they are a go/no-go operation — speed and stopping are the main considerations. In material handling operations, the induction motor is used for rudimentary positioning, but doesn’t allow for feedback when achieving maximum speed and stopping.
When tasked with an operation that requires more complicated accelerating and decelerating, the servo motor will perform better because it can catch up to the speed of the material faster than an induction motor, while producing more accurate positioning. Material handling equipment like stackers and nesters require positioning accuracy and therefore, use a servo motor. That is because servo motors are controlled by drives that are capable of creating complex motion profiles, like starting and stopping several times and robot control. They are also easily adaptable for handling multiple products.
Material Handling lines generally use a mix of induction and servo motors. Some examples of induction and servo motors include:
Induction motors with VFD
1. Conveyors
2. Pinch Rolls
3. Slitting systems
Servo Motors
1. Pick and Place
2. Squaring systems
3. Entry guides
People. Products. Passion.
The math required to manufacture any equipment in a roll forming line can be complicated. Engineers must accurately account for speed, material weight and product size. Some applications may require two or more servo motors for positioning larger products during material handling applications.
An experienced manufacturer will be able to walk you through the entire process ensuring that your machine meets your requirements effectively. It’s about engineering solutions and finding the optimal design for you.
Samco Machinery focuses on custom design and manufacturing because it recognizes that every customer has individual needs that require unique solutions. The extensive experience and passion of the Samco team strive to always provide innovative solutions and value-added services that surpass the customer’s expectations.
About the author:
Jim Harmer is an electrical designer working with Samco for nearly a decade. He has over twenty years of experience working with automation and controls in various industries including material handling, pharmaceutical and automotive. With extensive global travel, he has commissioned lines in over 15 countries and 6 continents.